Automating EV Battery Inspection and Traceability with Machine Vision
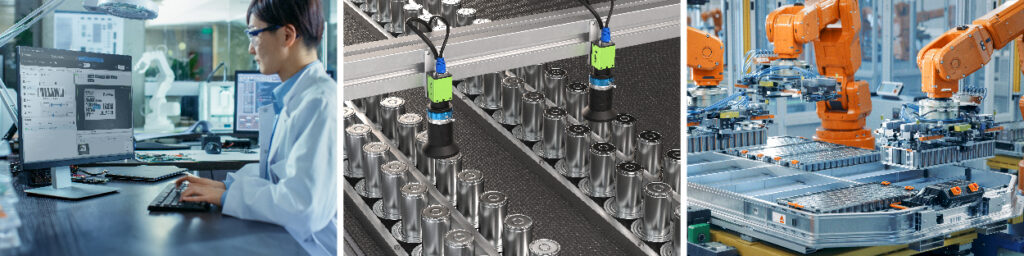
Battery manufacturing for electric vehicles (EVs) is one of the most exciting but challenging opportunities in the automotive industry. Rapidly increasing demand and the need to comply with rigorous quality standards both put strains on capacity, throughput, and quality assurance.
However, there are industrial automation and visual inspection technologies that can help EV battery manufacturers maximize high-quality production by enabling unprecedented traceability, quality, and greater automation in every production process.
One key way to do this is to adopt advanced machine vision solutions and integrate them across every stage of production. Using these sophisticated technologies and software, you can automatically and visually inspect, measure, and analyze all cell components and battery cells, cell stack and module assemblies, and battery pack assemblies—with maximum accuracy and efficiency.
Machine vision technologies are extremely powerful and high-resolution visual sensors and imagers that automatically capture, process and analyze images of target objects at high speeds and with extreme accuracy.
For example, with machine vision sensors from Zebra Technologies, each device can capture up to 16 images of each target object, even on high-speed production lines, and each image can have its own settings for everything from lighting to contrast, filters, edge detection, presence/absence detection, and more.
This automated image capture and analysis allows each device to be used as a data capture or visual inspection device. It can be used to scan and decode 1D/2D barcodes, direct part marks, or even optical characters, and it can also perform highly sophisticated visual sensors.
How Machine Vision Can Automate EV Battery Inspection Processes and Traceability
Here are some examples of how you can use Zebra machine vision to completely automate and error-proof traceability and visual inspections in your EV battery production and quality assurance. You can:
- Inspect battery cell component coatings for even thickness
- Check positioning and alignments of battery components and cells
- Detect defects and flaws in cells
- Measure tab and connector size and integrity
- Scan troublesome reflective surfaces
- Ensure uniform application of adhesives and thermal beads
- Check internal components for debris and structural integrity
- Perform final quality inspections
- Track and validate parts through assembly
- Ensure end-to-end traceability and lot tracking throughout your processes
For a detailed summary of EV battery production use cases and capabilities, you can download our mini eBook on Zebra Machine Vision for EV Battery Manufacturing. But here are a few specific EV batter manufacturing challenges that Zebra technologies have helped solve:
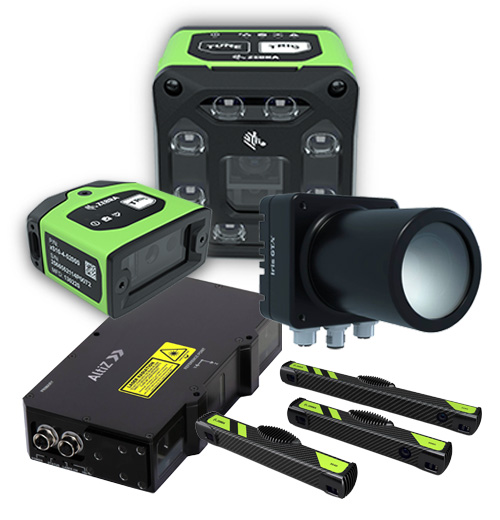
- With machine vision sensors, you can ensure that no scratches or holes are compromising battery cell integrity, using 3D imaging tools and deep-learning software to accurately detect defects before they move downstream in production.
- Zebra’s sensors and 2D code-reading tools can also be configured to identify electrode types and to log batch numbers for lot tracking, to help ensure safety and meet regulatory requirements.
- You can also use Zebra machine vision and its high-speed frame grabbers to detect the position and alignment of anode/cathode stracks.
- Additionally, you can use Zebra’s sensors, 3D profilers and vision software to ensure that cell components are accurately aligned in assembly battery modules.
These are just a handful of the more specific cutting-edge capabilities that machine vision tools such as Zebra sensors can provide—all with advanced vision technology that performs at levels far beyond the capabilities of the human eye. Importantly, as remarkable and sophisticated as these devices are, they’re also extremely easy to deploy, integrate, and configure with plug-and-play simplicity and easy-to-use software.
What Makes Zebra’s Machine Vision So Different and So Much Better
Each Zebra machine vision sensor is a compact device that fits virtually anywhere on manufacturing production lines and connects to manufacturing, automation and quality assurance systems via any standard industrial communication protocol, including TCP/IP, Serial, Profinet/Modbus, or CC Link. This allows you to easily transmit data to your systems and store captured and analyzed images for later review, analysis, or compliance recordkeeping. You can also power and connect your devices through USB-C, 24V DC, or Power over Ethernet (PoE), and there are hard-wired general-purpose inputs/outputs (GPIO) to give you huge flexibility in connectivity.
Unlike most other machine vision solutions, which are notorious for being rather difficult and time-consuming to set up, learn, and configure, Zebra’s devices and software were designed from the ground up to be accessible to users of any level. They enable both fixed industrial scanning and machine vision capabilities through one hardware and one modern software platform with an extremely simpler user interface, which dramatically shortens the learning curve and reduces hardware and software costs.
This is why Zebra devices have become one of our top-recommended industrial automation platforms for EV battery manufacturing and for key production and quality inspection processes across many other industries. As a system designer and integrator, we can attest to the fact that Zebra has not only enabled some really incredible automation and inspection capabilities for our customers, but it has made our lives a lot easier, too. It’s just much simpler and more affordable to work with these technologies, despite the world of process and inspection automation they enable for manufacturing.
To learn more about Zebra machine vision for EV battery manufacturing, download our mini eBook as a quick reference, and feel free to contact our industrial automation experts at Graftek Imaging. We’re always happy to answer questions, provide advice and recommendations, or explore opportunities to help you deploy solutions like these and automate more of what you do.

"*" indicates required fields